1 鋰離子電池發(fā)展背景
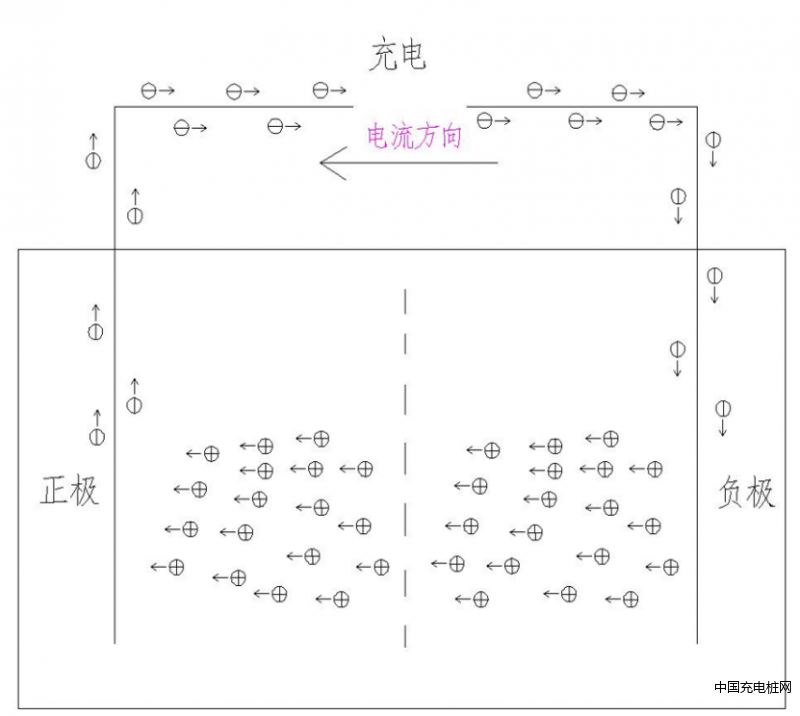
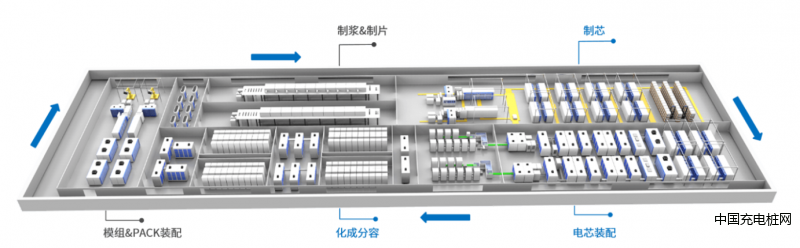
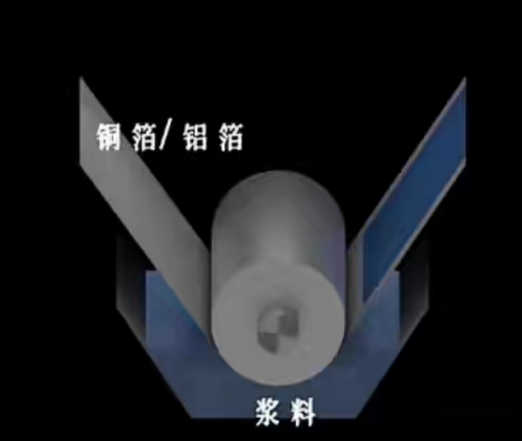
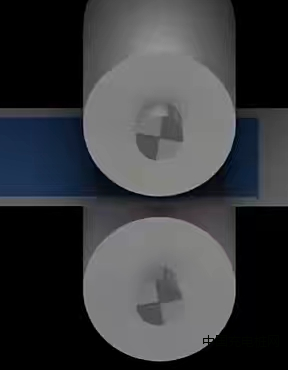
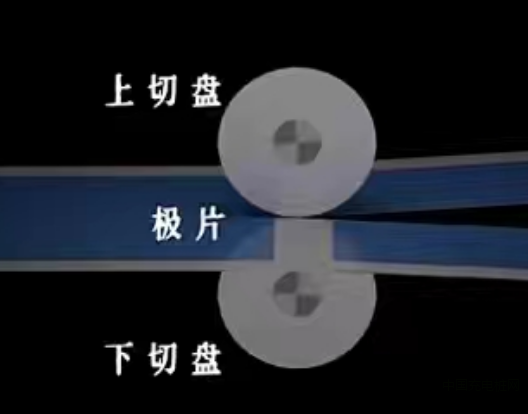

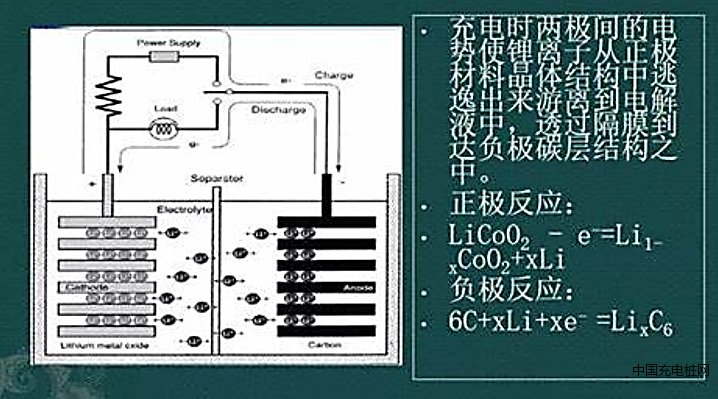
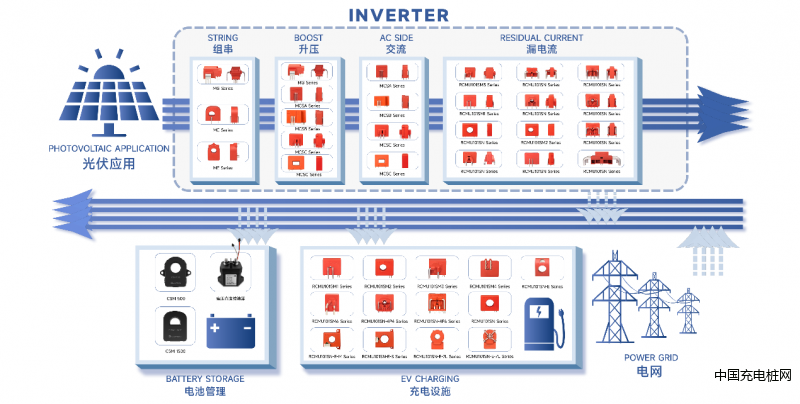
20世紀70年代初,鋰離子電池的出現(xiàn)給能源革命增添了一筆濃重的色彩。作為一種能量密度高、循環(huán)次數(shù)多、使用壽命長的新型二次電池,鋰離子電池被廣泛應(yīng)用于移動電源、電動車、家電、智能穿戴設(shè)備、3C產(chǎn)品等領(lǐng)域。
伴隨著2020年9月22日,我國提出的“碳中和”目標,政府陸續(xù)出臺了一系列政策措施,加強碳排放控制和可持續(xù)發(fā)展等方面的工作,并一直致力于推動全球應(yīng)對氣候變化的協(xié)同發(fā)展。截止2022年底,在中國新型儲能技術(shù)中,鋰離子電池儲能技術(shù)占據(jù)主導(dǎo)地位,占比高達93.7%,在新增儲能裝機項目中占比約為94%,是目前主流的儲能技術(shù)。
2022年全國汽車保有量3.19億輛,新能源汽車保有量達1310萬輛,同比增長67.13%,占汽車總量的4.10%。其中,純電動汽車保有量1045萬輛,占新能源汽車總量的79.78%呈高速增長態(tài)勢,電池作為電動汽車的核心部件,需求量呈高速增長態(tài)勢。
雙碳政策為鋰電行業(yè)帶來了巨大的投資機會和市場需求,也推動著鋰電技術(shù)的進步和發(fā)展。
2 鋰離子電池內(nèi)部構(gòu)造解析
實際應(yīng)用中,鋰電池按封裝方式主要分為圓柱,方形和軟包三種,其核心差異在外殼材料上及卷繞方式上。圓柱和方形電池主要采用金屬材料作為外殼,而軟包鋰電池采用鋁塑膜作為封裝外殼。
從結(jié)構(gòu)上分析,鋰電池都是由正極、負極、隔膜、電解液及外殼組成:
正極:主要有三元(NMC)、磷酸鐵鋰(LiFePO4) 、鈷酸鋰(LiCoO2)、錳酸鋰(LiMn2O4)幾個類型,其原理是充電時,鋰原子會分裂為鋰離子和電子,電子隨外圍電路回到負極,形成電流,放電時則相反;
負極:主流為碳基材料,起電子儲存跟釋放作用;
隔膜:一般為單層的PP(聚丙烯),PE(聚乙烯),也有雙層或PP/PE/PP三層復(fù)合隔膜,其主要功能是防止兩極接觸而發(fā)生短路同時使電解質(zhì)離子通過。其性能決定著電池的界面結(jié)構(gòu)、內(nèi)阻等,直接影響著電池的容量、循環(huán)以及電池的安全性能;
電解液:在正、負極之間起著輸送離子傳導(dǎo)電流的作用,并且只能通過離子,電子則不能通過,也是能量密度和功率密度的關(guān)鍵;
工作原理圖如圖1所示。
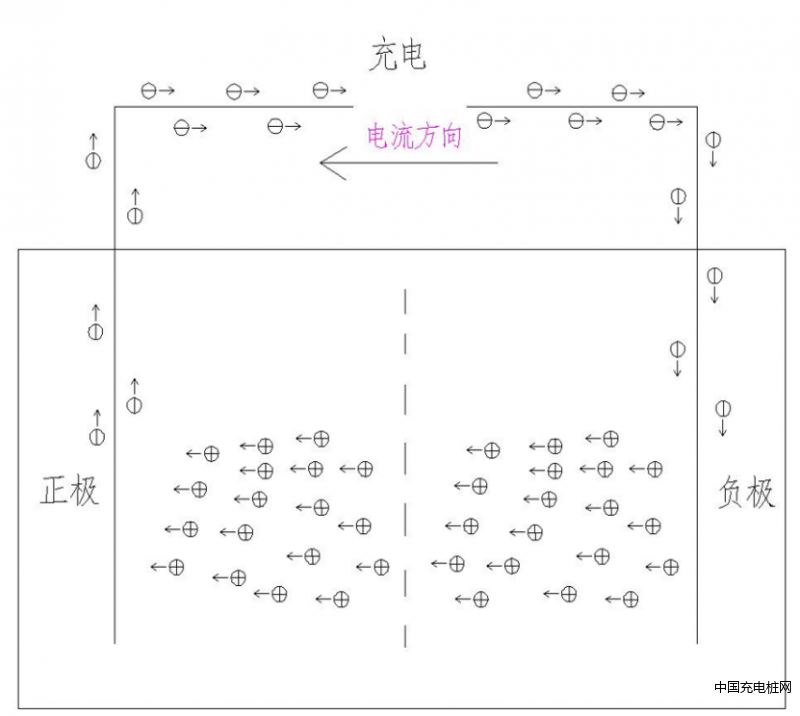
圖1 鋰電池工作原理圖
3 鋰離子電池的生產(chǎn)
在鋰電池生產(chǎn)中,最重要的就是正負極片的生產(chǎn)和電芯成型工藝。
正負極片是由導(dǎo)電片跟正負極漿料組成。鋰電池是將化學能轉(zhuǎn)化為電能的一種電化學裝置。在轉(zhuǎn)換過程中,我們需要一種介質(zhì)把化學能轉(zhuǎn)化的電能傳遞出來,即導(dǎo)電材料。而在導(dǎo)電材料中,金屬材料是導(dǎo)電性最好的,而在金屬材料里價格又便宜的就是銅箔和鋁箔。在電芯加工方面,主要有卷繞和疊片兩種方式。卷繞工藝需要用于制備電池的極片具有一定的柔軟性以保證極片在卷繞時不發(fā)生脆斷等問題。而金屬材料中,銅鋁箔也是質(zhì)地較軟的金屬,因此銅箔、鋁箔被廣泛應(yīng)用在電池的正負極導(dǎo)電材料中。鋰離子電池生產(chǎn)流程圖如圖2所示。
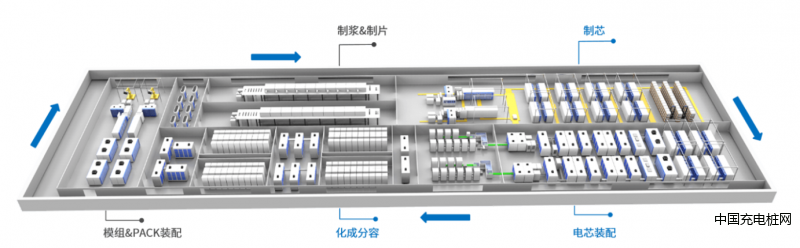
圖2 鋰離子電池生產(chǎn)流程圖
鋰電池生產(chǎn)第一道工序就是制漿,將正負極材料、黏結(jié)劑、導(dǎo)電劑充分攪拌形成正負極漿料,為了使材料混合均勻,需要嚴格控制攪拌的時間與方法,該工序控制的好壞將直接影響電池質(zhì)量跟成品合格率。
第二步就是將攪拌好的漿料按正負極均勻地涂到鋁箔、銅箔上。由于正極電位高,銅箔在高電位下很容易被氧化,而鋁的氧化電位高,并且鋁箔表層有致密的氧化膜,因此正極導(dǎo)電體為鋁箔,負極為銅箔;這道工序需要保證極片厚度和重量一致,否則會影響電池的一致性。涂布示意圖如圖3所示。
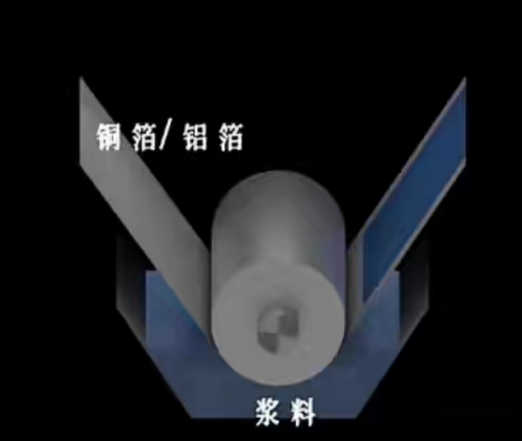
圖3 涂布示意圖
第三步是輥壓,將制好的極片放入輥壓機中進行輥壓,這也是增加能量密度的重要一環(huán)。輥壓示意圖如圖4所示。
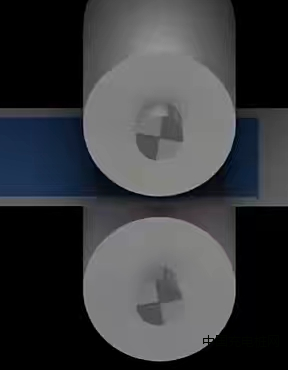
圖4 輥壓示意圖
第四步則是分切,按需要生產(chǎn)電池的尺寸將極片分切,分切過程中會有毛刺的產(chǎn)生,這種毛刺只能在顯微鏡下觀察到。為了避免毛刺扎穿隔膜,產(chǎn)生嚴重的安全隱患,此步驟需要嚴格管控毛刺的情況,到此正負極片的生產(chǎn)就算完成了。分切示意圖如圖5所示。
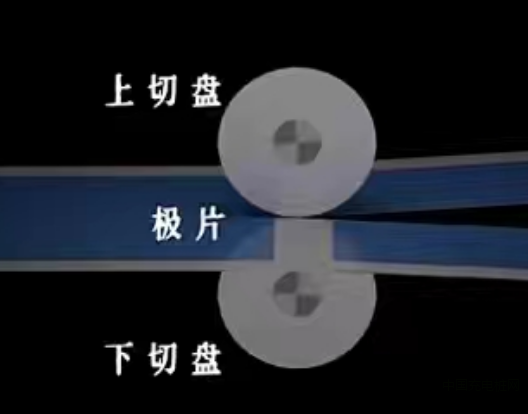
圖5 分切示意圖
接下來是電芯成型工藝,主要有兩種方式:卷繞法跟疊片法。卷繞法是按正極-隔膜-負極-隔膜的順序?qū)⒉牧暇砝@起來,形成裸電芯。需要使用先進的CCD視覺檢測設(shè)備完成自動檢測及自動糾偏,保證電芯極片不錯位;疊片法是按正極-隔膜-負極的順序疊加起來。卷繞法一般適用于圓柱電池、方形電池,疊片法則用于軟包電池。卷繞示意圖如圖6所示。

圖6 卷繞示意圖
之后將裸電芯放入外殼,進行電芯排氣,最后注入電解液并蓋上頂蓋封口。
4 鋰離子電池的激活與檢測
經(jīng)過前段工序,鋰電池的電芯功能結(jié)構(gòu)已經(jīng)形成,后續(xù)則是需要對其進行化成分容、檢測、分選、組裝,形成使用安全、性能穩(wěn)定的鋰電池成品?;稍韴D如圖7所示。
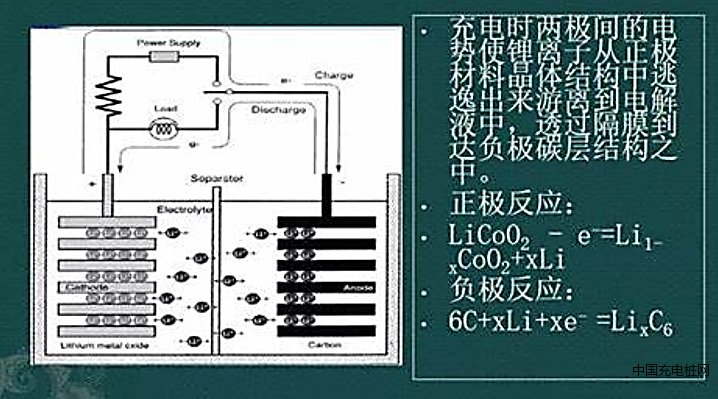
圖7 化成原理圖
其中,化成通過對高溫老化后的電池進行首次充電,激活電池,在負極表面形成SEI膜,就是在電極材料表面的一層膜,通過電解液消耗鋰離子形成,能夠有效阻擋電子和溶劑分子通過。
一般的步驟為:
(1)擱置:將電池組裝在針床化成柜上擱置5min;
(2)恒流充電:0.02C恒流充電至3.0V;
(3)擱置:擱置5min;
(4)恒流充電:0.05C、0.1C、0.15C恒流充電至3.5V;
(5)擱置:擱置5min;
(6)恒流放電:0.1C恒流放電,放電深度50%SOC;
(7)老化:常溫擱置15天;
以0.02C充電到3V,在SEI膜基本形成后以稍大一點電流充,不但節(jié)約更多時間;且形成的SEI膜致密,熱穩(wěn)定性更好,此時的SEI膜將電解液與石墨完全隔開,只許離子通過到達石墨層。
分容則是使用充放電機對電池進行充電放電,通過一定規(guī)范進行“充滿電-放完電”循環(huán),利用安時積分法確定電池的容量,也就是循環(huán)時間乘以放電電流得到的結(jié)果就是電池的容量。只有測試的容量滿足或大于設(shè)計容量的電池是合格的,并且需要保證電池的一致性。
經(jīng)過化成分容之后再利用OCV、DCIR等測試設(shè)備對電池開路電壓、交流內(nèi)阻、殼蓋絕緣等參數(shù)進行測量,篩選合格的單體電池,最后經(jīng)過高溫老化,就完成了電池的生產(chǎn)。
5 化成分容電流檢測方案
綜上所述,電流檢測技術(shù)對化成分容工藝具有重要作用。業(yè)內(nèi)化成分容產(chǎn)線的電流測量精度普遍在萬之五,其使用的電流測量方案主要有兩種:
5.1 傳感器方案
采用高精度閉環(huán)磁通門電流傳感器,現(xiàn)有的單電源、雙電源傳感器精度普遍在千一到千七之間,整體是無法達到產(chǎn)線的要求,那做化成分容產(chǎn)線的廠家都會搭建測量電路,根據(jù)傳感器線性度進行分段標定以及依據(jù)溫度曲線做補償,以達到目標的萬五精度,因其體積小、性能穩(wěn)定、價格便宜被廣泛應(yīng)用;另外現(xiàn)有的PPM精度級別的傳感器由于價格太高,更多是應(yīng)用在對產(chǎn)線的標定工作。
5.2 分流器方案
本身能達到較高的精度,但是溫漂較大,且本身功耗較大,因此目前主要在小電流場景或者加強散熱的環(huán)境下使用。
Magtron采用自主研發(fā)的的專利ifluxgate技術(shù)打造的高性價比、低零飄、高帶寬電流傳感器,可滿足化成分容產(chǎn)線使用,實現(xiàn)高精度的電流采集。由公司自主研發(fā)的SoC芯片也可以為客戶提供專有的技術(shù)解決方案,基于市場實時的最新需求,不斷升級完善,致力于解決工業(yè)、電動汽車、儲能行業(yè)等各項電流、漏電流采集問題,為各行業(yè)電力設(shè)備保駕護航。Magtron電流檢測方案如圖8所示。
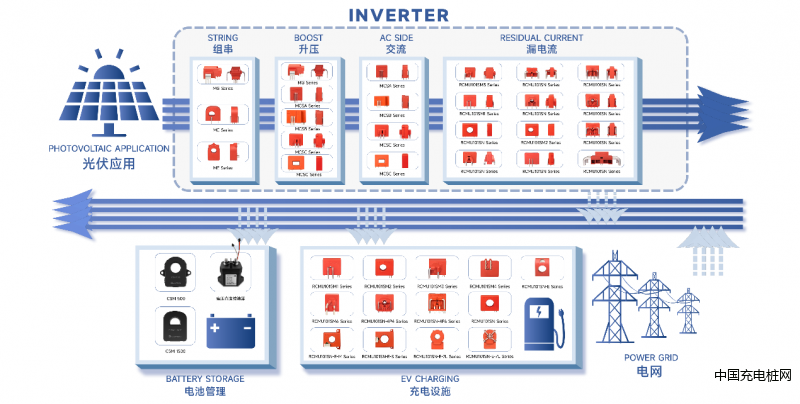
圖8 Magtron電流檢測方案
參考文獻:
[1]毛松科. 鋰離子電池生產(chǎn)工藝及其發(fā)展前景[J].
[2]葉霽萱,曲濤,趙宇鋒,等. 鋰離子電池正極材料LiFePO4高低溫性能研究[J].
[3]吳澤軼,操世鑫,王少鵬,等.快速充放電鋰離子電池負極材料開發(fā)[J].
[4]劉璐,王紅蕾,張志剛.鋰離子電池的工作原理及其主要材料[J].
[5]戴燕珊,冼巧妍,黃振茂.《鋰離子電池性能研究》
[6]胡廣俠,解晶瑩.影響鋰離子電池安全性的因素[J].
[7]杜翠薇,趙煜娟,吳蔭順,等.熱處理改進天然石墨的電化學性能[J].
[8]黃峰,周運鴻.鋰離子電池電解質(zhì)現(xiàn)狀與發(fā)展[J].